Workers at a Major Toyota Plant Are Looking to Unionize
This month, workers at a Toyota engine plant in Troy, Missouri, went public with their campaign to join the United Auto Workers. It’s the first announced campaign in UAW’s current union drive at Toyota, the world’s largest automaker.
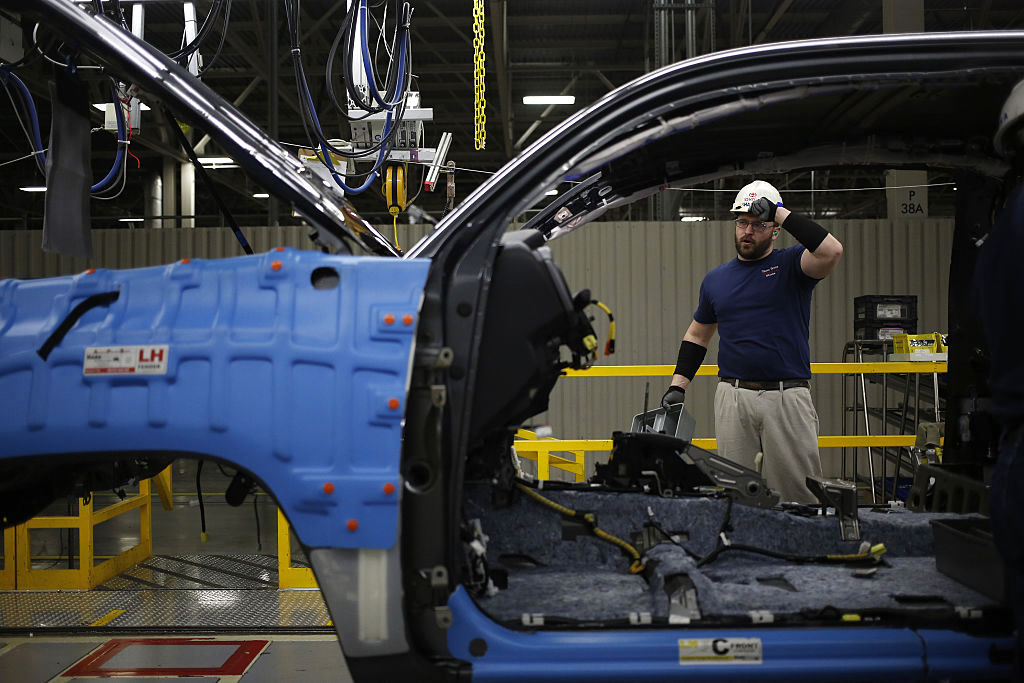
A worker on the assembly line at a Toyota manufacturing facility. (Luke Sharrett / Bloomberg via Getty Images)
Autoworkers at a Toyota engine plant in Troy, Missouri, have signed up 30 percent of their thousand coworkers to join the United Auto Workers (UAW) — a first at Toyota, the world’s largest automaker, on the heels of the union’s announcements of organizing campaigns at Volkswagen, Hyundai, and Mercedes-Benz.
Workers at the plant just outside St Louis build 2.6 million cylinder heads per year. Should they stop building them, it would cut off supplies for all of the company’s engine plants in North America. Toyota is still working to build up its supply of chips and other inventory, following pandemic lockdowns and global supply chain snarls.
In the body of a vehicle, these cylinder heads are as essential as human lungs, controlling the flow of air and fuel into the combustion chamber, powering a vehicle’s performance on the road.
In a new video released earlier this month, “We Keep Toyota Running,” workers describe the steep cost at which that performance comes. “People say Toyota engines last forever,” a worker says in the video. “We know what makes it possible: our hands, our backs, our knees, our work. We carry the proof every day: injuries, surgeries, disabilities.”
Time to Rest and Recover
Why are they joining the UAW? They want to take back their time to spend it with family, and rest and recover from injuries. “So our bodies can last as long as Toyota’s engines,” another worker says in the video.
Workers describe a grinding pace. They work ten- and twelve-hour schedules in sweltering temperatures that top 100 degrees Fahrenheit in the summer. The result is that their bodies break down — torn rotator cuffs, a common injury at the plant.
The work environment is also hazardous in other ways; one worker suffered a fractured skull, which has left her with excruciating migraine headaches.
“The plant is not safe,” said Jaye Hochuli, a team leader at the plant, in a press statement. “They had me crawl under a deck to clean out the sand and silica dust and chemicals that come out of the machines. It was a confined space. I should’ve been in a respirator and a hazmat suit. All they gave me was a KN95 mask. I came home and that dust was in my hair, on my clothes, in my underwear. How can the richest car company in the world not follow basic safety practices?”
Preemptive Wage Bumps
Workers told Labor Notes last October that Toyota had boosted wages to preempt the UAW’s organizing push. At an engine plant in Huntsville, Alabama, the company raised top pay to $32 and shortened the time to get there from eight years to four.
A worker at Toyota’s assembly complex in Georgetown, Kentucky, said the company was slashing the progression to top rate in half there too; the top rate increased by $2.94 to $34.80 for production workers and by $3.70 to $43.20 for skilled trades.
“The company has a slogan they like to use: One Toyota,” said Jarred Wehde, a production worker. “We’ve got the Toyota sign out front, just like they do in Kentucky and Indiana. But our pay is nowhere near what theirs is. We know what the company makes. We know they can afford to pay us.”
Even after a 9 percent wage bump, nonunion autoworkers in Troy are making $4 an hour less than their counterparts at equivalent union facilities, according to the UAW’s press release.
Equal With the Big Three
“Seeing the new contracts with the Big Three, that’s when I realized we needed a union,” said Charles Lashley, a team member at the plant. “It was incredible that UAW members could bargain for those benefits and that pay. I don’t see why we should be paid differently. Toyota makes more money than all the Big Three. So there’s no reason why we should be so far behind. The company can’t run without us. We should get paid like it.”
Toyota raised its full-year operating profit forecast by 9 percent, or $33 billion, last month. It sold 143,241 vehicles in the United States in January.
More than ten thousand workers across thirteen nonunion carmakers have signed union cards since last November, when the UAW announced an ambitious goal to organize 150,000 autoworkers. Public campaigns are underway at Volkswagen in Chattanooga, Tennessee, Mercedes in Vance, Alabama, and Hyundai in Montgomery, Alabama, and more than two dozen other facilities nationwide.